The performance of PE double-wall corrugated pipeThe three main performance indicators of PE double-wall corrugated...
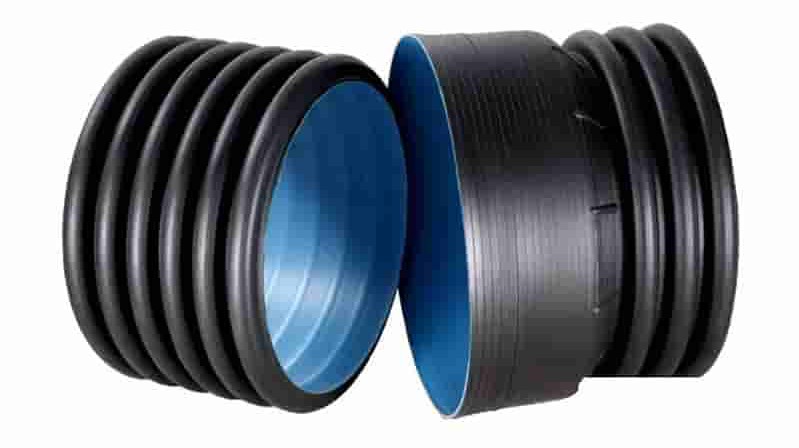
The performance and analysis of common shortcomings of PE double-wall corrugated pipe
The performance of PE double-wall corrugated pipe
The three main performance indicators of PE double-wall corrugated pipe: Ring stiffness, impact resistance, and ring flexibility.
- Ring stiffness: The ring stiffness represents the ability of the pipe to resist external pressure, and the unit is kN/m².The value of ring stiffness is larger, the stronger the resistance of the pipe to external pressure and the thicker the wall thickness of the corresponding pipe.
- Impact resistance: Using the method of drop weight impact, in the environment of 0±1℃, the true impact rate (TIR) is less than or equal to 10% (it can be understood that 10 pieces are allowed to break 1 piece, but they are not completely equivalent). The factors that affect impact resistance are similar to those that affect ring stiffness.
- Ring flexibility: The ring flexibility inspection equipment is the same as the ring stiffness, but the compression amount is larger. When the outer diameter deformation of the sample in the vertical direction is 30% of the original outer diameter, the load is immediately unloaded, and it is observed whether the inner wall of the sample remains smooth and whether there is reverse bending, whether it is broken, whether the two walls are disengaged. Ring flexibility reflects the ability of the pipe to resist deformation. In addition to ring stiffness, ring flexibility, and impact resistance, the standard also has a creep ratio (reflecting the creep of the PE double-wall corrugated pipe after deformation under external load, which affects the service life of the product) and oven test (reflecting the combination of the inner and outer walls of the PE double-wall corrugated pipe, whether the strength is sufficient and how stable is the structure) are required.
Common problems of PE double-wall corrugated pipe
The wave crest cannot be formed when it is just turned on, at this time, it is usually accompanied by the outer vacuum that cannot reach the required degree of vacuum. This is one of the most common phenomena in bellows production. The reasons are generally as follows:
- In terms of parameters, for example, the speed of the molding machine does not match the extrusion volume. If the extrusion volume remains unchanged, the material blank in the block will be too thick if the speed of the molding machine is too slow. Under the action of compressed air and vacuum negative pressure, the material blank cannot be attached to the inner surface of the molding block, it is difficult to shape. If the speed of the molding machine is too fast, the material blank will not be enough to fill the inner surface of the molding block, and the atmospheric pressure will enter the vacuum tank and molding will not be possible.
- In terms of raw materials: there are impurities in the raw materials; because some of the raw materials receive heat in the machine head for a long time, the raw materials are thermally degraded, lose their toughness, and are difficult to form; because the temperature of some sections is out of control, the temperature is too high, causing the materials to scorch, charred materials It will adhere to the surface of the molding block. During the extrusion process, some charred materials are sometimes entrained, and the blanks with coke materials cannot be formed. In addition, the overall temperature is too high and it is difficult to form.
- Mechanical aspects: the center line of the molding block and the center line of the water jacket deviate too much, so that the material on one side is severely dragged (torn) and cannot be formed; there is air leakage in the vacuum pipeline; the compressed air path is blocked; The interval between the two molding blocks is too large, etc.
Uneven inner wall
The uneven inner wall of PE double-wall corrugated pipe is usually caused by low vacuum degree, high water jacket temperature, and thin inner layer. If the vacuum degree is too small, you should check whether the inner vacuum pipeline is dredged and whether the vacuum pump is working normally. The high temperature of the water jacket is usually caused by the high temperature of the cooling water or the small flow of the cooling water, which can be dealt with by adjusting these two aspects.
Poor flaring
Poor flaring can be divided into the following conditions:
- The reason why the inner layer is blown is usually that the air pressure of the inner layer is too large; the material resistance is not good; the inner layer is too thin; The flared air inflation starts late or the flared air inflation pipeline is blocked; there are impurities in the raw materials; poor plasticization of the materials, etc.
- If the inner and outer layers of the flaring are not properly attached, if this phenomenon occurs at the beginning, it is due to the air inflation late start of the inner layer or the air pressure in the corresponding section is too low; if it occurs at the end, the air inflation of the inner layer end prematurely or the flaring deflation ends early, or it may be because the air pressure in the corresponding section is too low; if it is not pasted from beginning to end, it may be due to the function of the material or the temperature. If it is not pasted from beginning to end, it may be due to the performance of the material or the temperature.
- The flaring is not complete, and the end of the flaring cannot be attached no matter how it is adjusted. Its reason is usually that the inner layer air inflation ends early, and the flaring deflation ends early.
- The inner layer at the front end of the flaring has a depression, which is generally caused by the air inflation premature start of the inner layer; the water jacket has deviated from the centerline of the molding block (the forming machine is not aligned with the water jacket); the inner layer wall thickness is too thin; The inner vacuum stops prematurely.
- The inner layer of the flaring end is material piled up, and this phenomenon often causes the flaring to be concave inward. The reason is that the inner layer material at the end of the flaring is too thick; the speed reduction of the forming machine in this section is too large; the inner layer air inflation of the previous sections is too large; the material temperature of the inner layer is too high, so the blank is too soft; The material blank of the outer layer is too thick in this segment.
There are scratches on the inner layer
Usually, due to the high temperature of the material, there are charred materials on the inner die; there are impurities in the material, scratches on the water jacket, scratches on the inner die, etc.
Outer wall with small holes
The reason is that there are impurities in the material; the temperature of a certain section is out of control, causing the material to scorch, and charred materials are sometimes taken out; In order to improve the performance of the pipe, some such as functional masterbatch, defoaming agent, etc., have poor dispersibility, it may be said that the compatibility with resin is not good.
The crest of the pipe is skewed
It is caused by the molding machine speed being too fast and the cooling is not good, and the normal air pressure is too small.
The weight of the pipe is not stable
Generally, it is because the performance of raw materials is unstable or the temperature of the feeding section fluctuates too much.
Pipe twists
The reason is that the partial wall of the outer layer is severe or the alignment between the water jacket and the forming machine is not well adjusted.
The inconsistent thickness of the crests in the axial direction
The normal air inflation is too large, the gap of the die is too large, etc.
The brittleness of the pipe after cooling is a relatively common phenomenon
Mainly due to poor performance of raw materials, such as the excessive proportion of fillers, poor quality of defoamer, excessive moisture content in raw materials, etc.
All the above pipe problems in the production process remind business owners who want to buy double-wall corrugated pipe equipment. The quality of the equipment is very important for the smooth production of qualified products. There are many manufacturers in China today that claim to be able to manufacture high-quality double-wall corrugated pipe equipment. For buyers who do not understand the state of the Chinese market, how to choose the right supplier to avoid falling into the trap is a huge challenge. Because not all manufacturers have research and development capabilities, and the company’s mission also affects the final equipment quality, if the company’s mission is to make quick money, buyers will inevitably face constant trouble in the life of the equipment if they buy the equipment they manufacture.
Please stay relaxed, Chnic can help you to simplify all processes!
If you are sure of the machine you require, simply email us and we will offer from factories that supply reliable and high-quality equipment.
If you are unsure of what you require, please email us with your job details and our engineering department will determine the ideal solution for your work. We will then offer the right product to give the most efficient production solutions for your project.
Need help sourcing machinery?
Chnic as an integrator helps wholesalers and factory owners one-stop equipping or updating their manufacturing facilities through top-end turnkey manufacturing.